A case study of MATSUMOTO PRINTING CO., LTD. installing our JFX200-2513 and CG-60SRIII was featured in the “Business now” on “Label Shimbun” (No. 1251 issued on September 1, 2021), the only label-related newspaper in Japan.
The following is the published article in its original form.
Click here for the original article PDF
MATSUMOTO PRINTING CO., LTD. (Kataoka, Yoshida-cho, Haibara-gun, Shizuoka, Japan; President Kenji Matsumoto; Phone 0548-32-0850) was founded in 1932 as a bag manufacturer. Later, the company expanded its business to the printing field and was established in 1961 under its current name. In addition to sheet-fed and web offset press printing, the company has been engaged in form printing since its early days, and is also good at handling variable data. The company has also promoted the digitization of prepress and print since the early times of the printing industry. As part of this effort, the company has achieved in-house production of labels using inkjet printers (IJPs) and digital printing machines. This is a report on the future of the printing industry from the viewpoint of the 89-year-old general printing company. (by Suzuki)
General printing company that provides a one-stop service

Kenji Matsumoto, President
The company is a locally based company with 80% direct business and 80% sales in the prefecture, and has 180 employees as a general printing company supporting the industries in the prefecture. Currently, the company has five sales offices, four in Shizuoka Prefecture and one in Tokyo, and manufacturing departments are concentrated in the Kawashiri factory in Yoshida-cho, where 118 employees, more than half of the total workforce, are working.
The Kawashiri factory, located near the head office, was established in 1990 after the first phase of construction was completed, because the head office factory became too small due to business expansion. It started the web offset press, and operations of the prepress department and rotary form printing department began. In the second phase of construction in 1994, all printing departments were moved from the head office to the Kawashiri factory to centralize the production process.
The company also started digitization early in the printing industry. In 1993, as the first step, the company built a unique digital prepress environment where all kinds of prepress can be connected to the in-house network. In 1999, as the second step, it realized the digitization of printing. By introducing E-Print 1000 by Indigo (at that time), etc., the company began receiving orders online to quickly respond to the needs of the times.
Later, the Kawashiri factory completed the third phase of construction in 2002 and established a new production system in response to increased orders. In order to enhance the digital printing environment, the company has added various sheet-type digital printing machines such as electrophotographic ones and UVIJs, as well as digital label printing machines, UVIJPs, and other printing machines and post-processing machines including large cutting plotters and laser die-cutting machines for different printing applications. On the other hand, conventional machines were replaced at an early stage based on a serious assessment of current demand and future potential. As a result of these reforms, the printing field is now divided into three main categories: “offset printing” for forms, commercial printing, envelopes, etc., partially in-house “label printing” that started in 2013, and “on-demand printing” for various types of small-lot print. The print store “Issaku-ya”, the company opened in 2014, is a mail-order site based on the concept of “original goods acceptable from one piece”, where you can consult about printed materials. It provides small-lot products mainly created by the UVIJPs of Mimaki Engineering (hereinafter “Mimaki”). Moreover, it also creates websites, videos, and digital books for companies, stores, organizations, hospitals and other industry sectors, as digital solutions that result in non-printed materials.
After starting out as a bag manufacturer, the company has expanded its business to commercial printing, forms and digital printing, etc., by keeping up with the changing times. President Matsumoto says: “We've been a typical order-taking company for a long time, but now that we have the machinery and human resources, we'd like to develop as a proposal-based company that undertakes not only printing but also event planning in whole, to help revitalize the region.” Wishing to promote what the company can do for its customers and the way of giving shape to their ideas, he aims for a company that provides a community-based one-stop service.
Occasional renewal toward the business optimized for the current trend
Proactive renewal of facilities
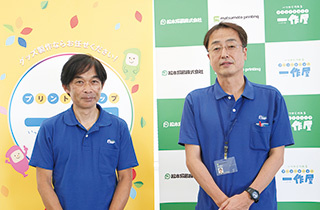
Akiyoshi Suzuki, Director and Manager of Kawashiri Factory, and Masahiko Ishikawa, EC Project Manager
“We were in a transitional period when demand for flyers declined as the times changed, and it was also a time to review our facility system,” says Factory Manager Akiyoshi Suzuki. The company has made wise decisions, not only at that time but in the 89 years since its foundation, for several major facility upgrades and business changes due to discontinuation while considering the age of printing equipment.
Firstly, for a sharp drop in demand for flyers and pamphlets, the company introduced digital printing equipment, which allowed it to achieve super short delivery time, enabling to deliver a small lot up to about 10,000 copies the day after receiving an order. “We were able to do this because we have an integrated production system, but now we have a lot of employees, so it's tough to get the right number of orders,” says Mr. Suzuki. However, since the company has about 3,000 customers through sales activities that have long been rooted in the local community, the decline in orders has been minimized even during the Covid-19 pandemic. “We actively respond to small-lot printing,” says Mr. Suzuki. “And we use digital machines as much as possible.”
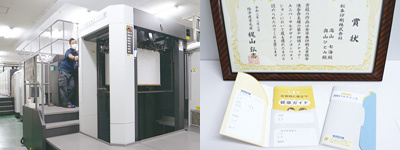
Latest full kiku size double-side sheet-fed offset press. Printed materials that received the METI Minister Award for MUD (Media Universal Design Competition)
On the other hand, for conventional machines, the company promoted a new challenge 16 years ago. In order to produce high-grade commercial printing with added value, such as clear printing and pseudo embossing, the company introduced Hidelberg's ten-color UV offset press (print size 636 x 939 mm) for the first time in Japan. However, although they have tried a variety of printed materials, due to the high barrier of the “price over quality” need fixed in the market, the situation has been tough in terms of generating cost effectiveness.
So, the company has shifted from form printing in which it has been engaged since its establishment. The company has been well known as “Matsumoto Printing of form printing” in the community, but with the spread of personal computers and the Internet, the demand for slips dropped dramatically. That was when the company decided to take on the challenge of label printing as a completely new manufacturing department.
Anything from film products to labels using digital machines
In-house label printing
Although the company had been selling stickers and labels in the past, they were 100% outsourced to a nearby label printing company. However, as a result of searching for an alternative to form printing, for which orders had decreased year after year, the company decided to partially produce labels in-house.
According to EC Project Manager Masahiko Ishikawa, Mimaki’s IJP was introduced in 2013. The machine is an excellent match for small-lot label production. The company also installs cutting plotters to manufacture name stickers ordered by elementary schools for new first graders, as well as stickers and labels ordered through a label app for consumers.
In 2016, to increase the rate of in-house production, Epson’s SurePress L-4033AW was installed. For die-cutting, the company has introduced laser die-cutting equipment from a neighboring manufacturer (Shinohara Japan at that time) in addition to Mimaki's cutting plotters to handle all processes digitally from printing to die-cutting.
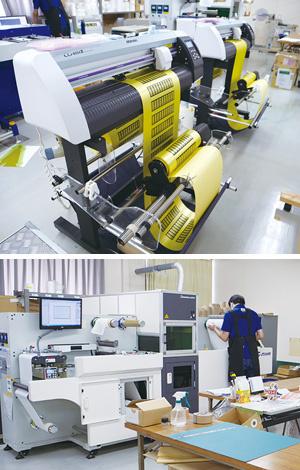
Mimaki’s cutting plotters (above) and laser die-cutting equipment (Kobundo) are used to cut labels after digital printing
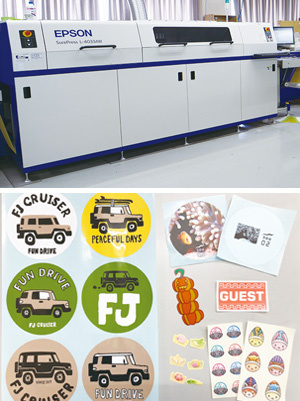
Introducing a digital label printing machine to increase the rate of in-house label production (above). Label product lineup that meets all customer needs
How did a general printing company, a beginner in label manufacturing, smoothly achieve in-house production of labels? In fact, the company does not manufacture all the ordered labels, but sorts out those that can be manufactured with its own digital equipment and those that cannot, and produces about 30% of them in-house. The neighborhood is a nationally famous production area for shirasu (whitebait), unagi (eel), and tea leaf and is rich in agricultural and marine products. So, “small-lot labels are a perfect match for digital machines,” says Mr. Ishikawa. On the other hand, of the shift from forms to labels, “Our printing volume, which had been rapidly declining, has steadily increased since we started label production, so we can only say, ‘thank goodness’,” Mr. Suzuki says with smile.
As for the operation of the SurePress, after studying at a label printing company, Mr. Ishikawa “worked steadily to adjust the color management to our own color profile.” Currently, Mimaki’s seven IJPs and five cutting plotters are installed. Not only labels but also all kinds of products such as signs, partitions, store displays, fixtures, and mail-order products are manufactured.
According to Mr. Ishikawa, the company has very capable operators, and its strength lies in the fact that it does not rely on manufacturers, but strictly implements its own ink drop control to produce high-quality printed materials that are unmatched by other companies. For this reason, the company promotes strict quality control even for digital prints at the level of sheet-fed offset press, looking through a magnifier. Even a printed signage to be seen from afar “still has good color and quality when seen up close, which is our selling point,” says Mr. Ishikawa. As for the future outlook, he is willing to “increase the number of small IJPs instead of large digital label printers, in terms of investment and workability, and strengthen our mobility.”
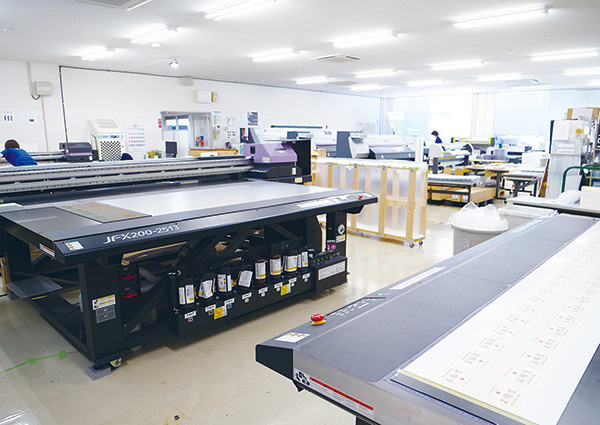
A total of 12 Mimaki’s IJPs and cutting plotters, ranging from small to large, are used for various digital prints
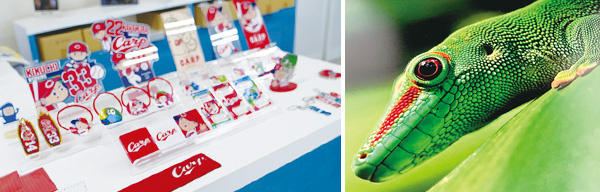
Original goods for the “Carp Baseball Gallery” of the Hiroshima Toyo Carp manufactured with Mimaki's IJP (left), and a print that successfully expresses realistic image using the 2.5D printing technology of the same IJP
Giving shape to every need
“We need to be a company that can do anything,” says Mr. Suzuki. Today, as the quality of various equipment has improved and any printing company can produce almost the same products, how to add value is the key to the company's survival. “As the times change, the definition of general printing also changes. While keeping printing as our core business, it is important to decide what to tackle newly,” he says. In fact, the introduction of the digital label printing machine was not disclosed for two years, but “we cannot grow if we keep internal information closed. In order to coexist, we must share information with our customers. It is my job to create new business departments, and the stickers/labels department is one of them,” says Mr. Suzuki.
On the other hand, President Matsumoto says that it is all about how to find a way for the company to survive in the face of declining sales due to a significant decrease in events caused by the coronavirus pandemic. “We create our own products and sell them ourselves, not only to businesses but also to consumers. We need to attack areas that the general printing industry has not targeted in the past.” As part of this effort, the company's mail-order print website will be reopened in December. The way the website is presented will be drastically changed to make it more customer-oriented for both businesses and consumers.
Matsumoto Printing is not just engaged in printing, but is trying to discover a business that benefits customers and connect it to printing. “What we can sell is changing rapidly with the changing times. So, we have to create business by ourselves from the ideas we received from customers and give shape to their needs. That's the most important,” says Mr. Matsumoto, but he also cites the issue of how to preserve the advantages of analog as another path to take: “Today's production process tends to go digital because of its speed and flexibility, but that's why I want to identify the technology and approach that only offset operators can preserve, and add value to them.” Another future is also in sight.
Source: Label Shimbun No.1251 issued on September 1, 2021.
User profile
- NameMATSUMOTO PRINTING CO.,LTD
- IndustryGeneral printing-related services (from planning to delivery), planning and production of websites, AR, video, and CD-ROM, sales of sales promotion products, advertising and publicity services, sales of OA equipment and software, and EC site operation
- Address2210 Kataoka, Yoshida-cho, Haibara-gun, Shizuoka, Japan
- Phone number+81-548-32-0850
- URLhttp://www.m-print.co.jp/